Over the past two decades Nuvation Engineering has developed data acquisition systems for a wide range devices and market applications. Based on our experience performing hundreds of engineering design projects, our engineers have identified several key considerations that require special attention during the planning, design, and development of data acquisition systems.
Designing for Space
Products designed for space are exposed to the some of the harshest environments. They must operate reliably under intense vibration, mechanical shock, wide temperature swings, a vacuum environment, and exposure to ionizing radiation. This article will share some of the solutions Nuvation Engineering implemented for outer space environments when we designed a 24-channel data recorder module for a spacecraft built by Space Systems Loral (SSL).
"Effective web design is akin to composing a symphony, it harmonizes aesthetics, functionality, and user experience into a seamless melody that resonates with every visitor.”
For short-term space missions (one year or less), it is sometimes permissible to use standard commercial-off-the-shelf (a.k.a. “COTS”) components in your design, subject to analysis and testing of their radiation tolerance. This can dramatically reduce the cost of designing space equipment and expand the selection of components available for the design.
Nuvation’s spacecraft design utilized mostly COTS components and included a few rad-hard parts for critical safety functions. We achieved this cost optimization in component selection by applying several design techniques in hardware and software to deal with the effects of radiation, such as:
The implementation of these design approaches in combination with the inclusion of a few rad-hard components dramatically reduced the potential risks associated with the effects of radiation damage.
A vacuum has a tendency to cause trapped gasses to leak from components or materials, an effect called outgassing. Since these gasses could interfere with other sensors or equipment on the spacecraft, all components on the PCBA had to be selected based on their outgassing potential. Nuvation’s engineering team also coated the board with a special low-outgassing, space-rated conformal sealant, which provided the additional benefit of protecting the PCBA from contamination during ground operations.
Nuvation Engineering worked with Space Systems Lorel to develop a system that was used to measure the shock and vibrations that occur when a spacecraft separates on its way into space.
Harsh Environments on Earth
Although space is a harsh environment, some of the harshest environments can be found right here on Earth. Every year, a number of Nuvation engineers contribute to the design and construction of TechnoGecko, an electric and autonomously driving mutant vehicle that is brought to the Nevada desert for one week. The daytime temperatures can reach 40°C (~104°F) and dip below freezing at night. The vehicle is exposed to high levels of vibration from the rough roads, and lack thereof. There are dust storms that coat everything in a thin layer of dirt. The electronics have to be designed to withstand wide temperature swings (including high temperatures generated by the vehicle itself) and high levels of vibration. Continuous reliable operation of the vehicle is critical given the remote location and dangerous conditions of any desert. Attention to design details, such as incorporating dust-proof connectors/enclosures to keep dust/water away from the electronics, contribute to ensuring reliability in the field.
It is important to realize that the end-users of your product may be exposing it to less-than-ideal conditions. When commissioning a battery management system for a grid-scale energy storage system, Nuvation engineers found that the radiated electrical noise from the power conversion system was significant enough to bring about the dreaded Blue Screen of Death on laptops that were simply in the same room as the noisy system.
Setting Design Requirements
Documenting requirements at the start of the project helps avoid major architecture and design changes later on. Understanding requirements and constraints allows our engineers to provide optimal architecture and design implementation options. Getting these details flushed out early makes for more efficient and cost-effective project execution. It is important that the Product Requirements Document specifies the product’s environmental requirements. Questions that should be answered in the PRD include:
When in Doubt, Do a Phase 0
The answers to the above questions are used to generate design requirements that will impact the success or failure of the product as much as (and in a harsh environment, perhaps even more than) application-level functionality. Trade-off decisions can usually be made that balance cost, functionality, operating range, and performance to yield a viable product that meets the desired price point. At Nuvation Engineering we refer to this level of up-front investigation as a Phase 0, a low-cost engineering investigation that enables the client to determine the viability and even desirability of the project effort before moving ahead. Often a slight modification to the product requirements (e.g. do you really need 4K video at 120 fps or is unit cost the higher priority) can alter the components and design requirements sufficiently to make the project more viable. Alternately, if the Phase 0 verifies that the product requirements are fully viable as-is, the documentation generated from that effort gets rolled into Phase 1 of the project planning documentation and can be referenced when generating the Bill of Materials (BOM) and design approach. For highly complex projects with technological risk (i.e. doing things that have never been done before, or in a way that has never been tried before), a Phase 0 provides engineering validation of viability and proposes design approaches the client can utilize to verify budgets and determine next steps.
Making Environments Friendlier
- Tighten the operating temperature rating of your product (your product may not need to be designed for temperatures up to +125°C if you specify to users that it must be operated below +85°C).
- Choose whether heating circuitry, cooling circuitry, or both, are required to manage the temperature of the circuit board.
- Design the circuit board with components that can withstand a wide temperature range.
The right decision is very situation-dependent. Quite often, a decision matrix is used to determine the best design decision by rating the degree to which the design balances a range of factors such as cost, performance, reliability, operating range, etc. (see Figure 1).

Summary
Regardless of whether you’re designing a TV remote or a satellite system component, the engineering planning effort revolves around the same planning decisions.
When employing an engineering services company to assist with your product development effort, the ability of the service provider to manage the points in the above list should be part of key selection criteria, in addition to technical capability. With over twenty years of experience and a thousand projects completed, the Nuvation Engineering team can provide you with a range of viable options to deliver a high quality product designed to withstand its target environment, at a production price point that supports your business case. If your requirements and target price point are too far apart, we will help you discover that before any engineering work has been done, and explore ways to refine your product requirements to bring them into the realm of possibility from a design, technology and business case perspective.
Contact us for a quote on how we can help design your next product to withstand harsh environments, or simply the harshness of everyday living.
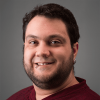