A client in the industrial automation industry chose Nuvation Engineering to design a custom sensor solution, processing board and algorithm, and web interface for a never before seen electrostatic braking system.
The manufacturing and logistics market spends up to 80% of their time on material handling. It is expensive, labour intensive and can be difficult to automate. This client developed a system that channels the same static cling that makes a balloon stick to your hair and combined this with machine learning software, allowing the system to handle virtually any material.
Nuvation Engineering designed the electrostatic braking communication and control system which intelligently slows, positions, and holds non-uniform cargo in an orderly queue on a gravity-fed load lane (free-rolling conveyer). This sensor solution helps prevent product damage and worker injury, all in poor lighting/fog, without cameras, and >1kV electrical switching noise in close proximity to the control modules. Nuvation Engineering also developed the web interface which displays system status (lane occupancy, faults, temperature, and humidity) and permits control of the electroadhesion technology in different sections of the load lane.
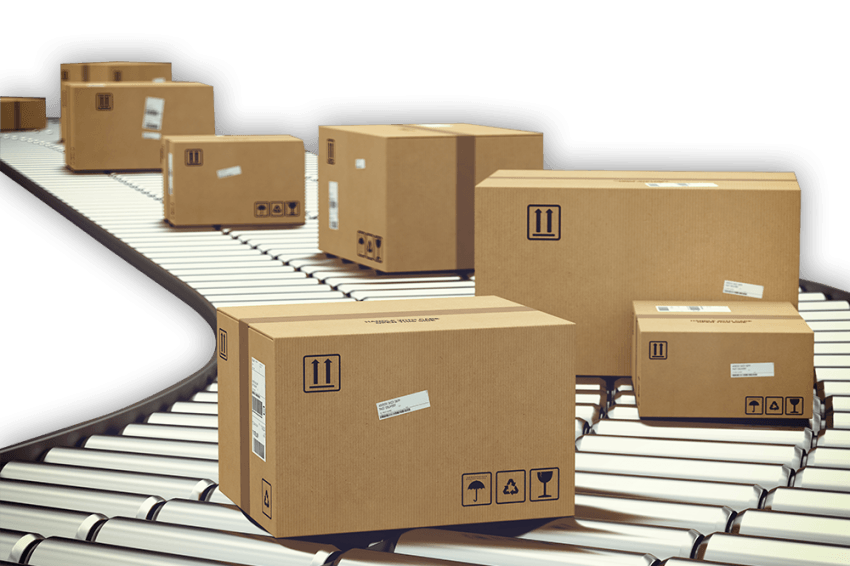
Design Features:
- >1kV electrical switching noise
- Safety oriented RS485 control protocol with fast (>50Hz) update rate
- Custom in-lane optical sensor network
- Integration with LIDAR, Stacklight Pole, E-Stop
- Custom algorithm for lane occupancy fill/drain
- Web Interface for status, logging, and control
Services Provided: